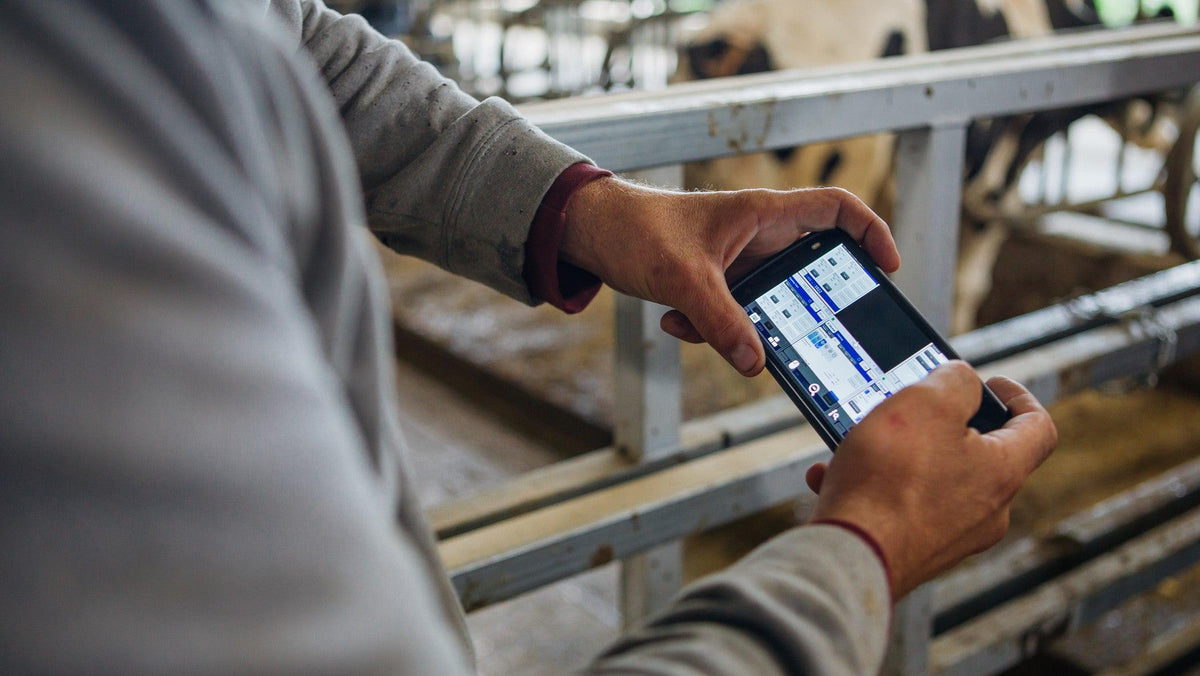
FarmLove – Foster Brothers Farm | Sustainability
Bob Foster has been on the leading edge of dairy diversification since the early 1980s. He coined the term “Cow Power” when he saw the opportunity to source clean-burning, environmentally safe, abundant energy from right under his feet…literally. The Fosters were the first in Vermont to install an anaerobic digester on their Middlebury dairy farm, where today they milk 440 cows and crop almost 2,000 acres. It produced electricity through generators powered by the methane gas released from treated cow manure, which they initially sold to their local utility and later used on the farm.

A byproduct of the digesting process inspired another business. The family has since built one of the region’s largest manure-based compost companies, producing and marketing a line of gardening and landscaping products sold around the Northeast. Eight members of the fourth and fifth generation of Fosters work together on the farm and the company called Vermont Natural Ag Products whose signature product is MooDoo® organic, composted cow manure. “It was a way of making better use of nutrients. The whole concept is to close the loop,” says Bob. “I enjoy the thought that we are converting solar energy into food, fiber and energy to nourish animals, plants, and people in an environment that directly involves family.”

They now source manure from other farms, along with other inputs like food scraps and leaf and yard waste from the local solid waste district, old round hay bales and sawdust. “Part of it is using materials other people call waste. We’re helping the environment as well as ourselves,” Bob says. “In the current lexicon, it’s what they call sustainable.”

The road to innovation has not always been smooth, Bob acknowledges with a smile: “You can make mistakes, but you’d better learn from them.” But the Fosters continue to stay ahead of the curve as was evident on a recent tour of the compost facility, which was busy heading into its peak season. On the dairy farm, the family uses cover crops and no-till practices to help maintain the vitality and integrity of the soil and minimize runoff and soil erosion.

On the compost side, Bob was happy to show off a specialized piece of equipment called a “turner,” the second Komptech machine (pictured in the image below) to be sold in the United States, that was making its way down a long windrow of compost-in-process, churning the rich mixture and releasing billows of vapor and heat. The machine can turn all the compost piled on the nearly 15-acre compost pad in six hours.

Another cool composting concept is the ‘Hot Box’. The Fosters received a USDA grant which enabled them to partner with Agrilab Technologies to build a heat recovery system at their compost facility. The next step, Bob said, is to capture all that vapor through the system (using the piping running through the tunnel seen in the image above). Early trials piping it out of a few windrows into a heat exchanger have so far heated one of their production plant buildings through the winter. “It’s all about addressing climate change,” Bob says. “We’re doing our little part.”

Let the Gardens Begin!
If you’re getting your garden ready for the season, head over to MooDoo® for some tips!